FONDERIE BASSE PRESSION
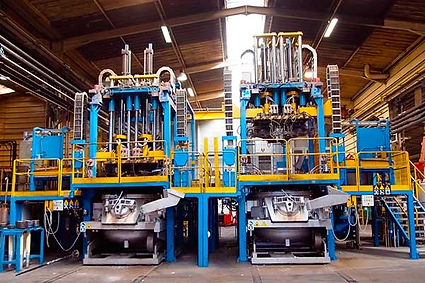
La coulée basse pression, aussi connue sous le nom de Low Pressure Die Casting (LPDC), est un procédé de fonderie qui consiste à remplir une coquille par une faible pression. Le métal en fusion est injecté par le bas du moule grâce à un four pressurisé générant un gaz neutre dont la pression est légèrement supérieure à la pression atmosphérique (1 bar maximum). De ce fait, le métal remonte verticalement et lentement dans un tube en céramique jusque dans la cavité.
Avant la coulée, dans le cas de moules permanents, l’empreinte peut être enduite de poteyage pour protéger l’outillage et favoriser la qualité de la pièce finale. Un noyau ou des broches peuvent être ajoutées à l’intérieur pour réaliser des formes internes
​
La faible pression générée par le gaz engendre un écoulement lent et régulier du métal dans toute l’empreinte. Ce procédé est donc adapté aux pièces à géométrie complexe et aux parois fines. Il est plus précis que le moulage sous pression.
Comparé à d’autres procédés de fonderie tel que le moulage en coquille par gravité, il garantit un niveau de qualité plus élevé. L’air s’échappant petit à petit par le haut du moule et la cavité pouvant être remplie progressivement, les risques de porosité et d’inclusions sont moindres.
Le moulage basse pression est principalement appliqué pour la fabrication de pièces en aluminium. Il est couramment utilisé pour la fabrication de pièces volumineuses comme des organes de direction ou bras de suspension et jantes pour l’industrie automobile, des pièces de structure pour l’industrie aéronautique, etc.
​
​
​